CENTRIC ⦁ HIT
CENTRIC ⦁ HIT - TECHNOLOGY revolutionises the piling process by making the pile driving faster, more efficient and more powerful. This innovative technology ensures that the pile is precisely centred, which means that the vibrations are transferred directly to the pile without any losses. The precise transmission of vibrations optimises the piling process, maximises overall performance and increases energy efficiency.
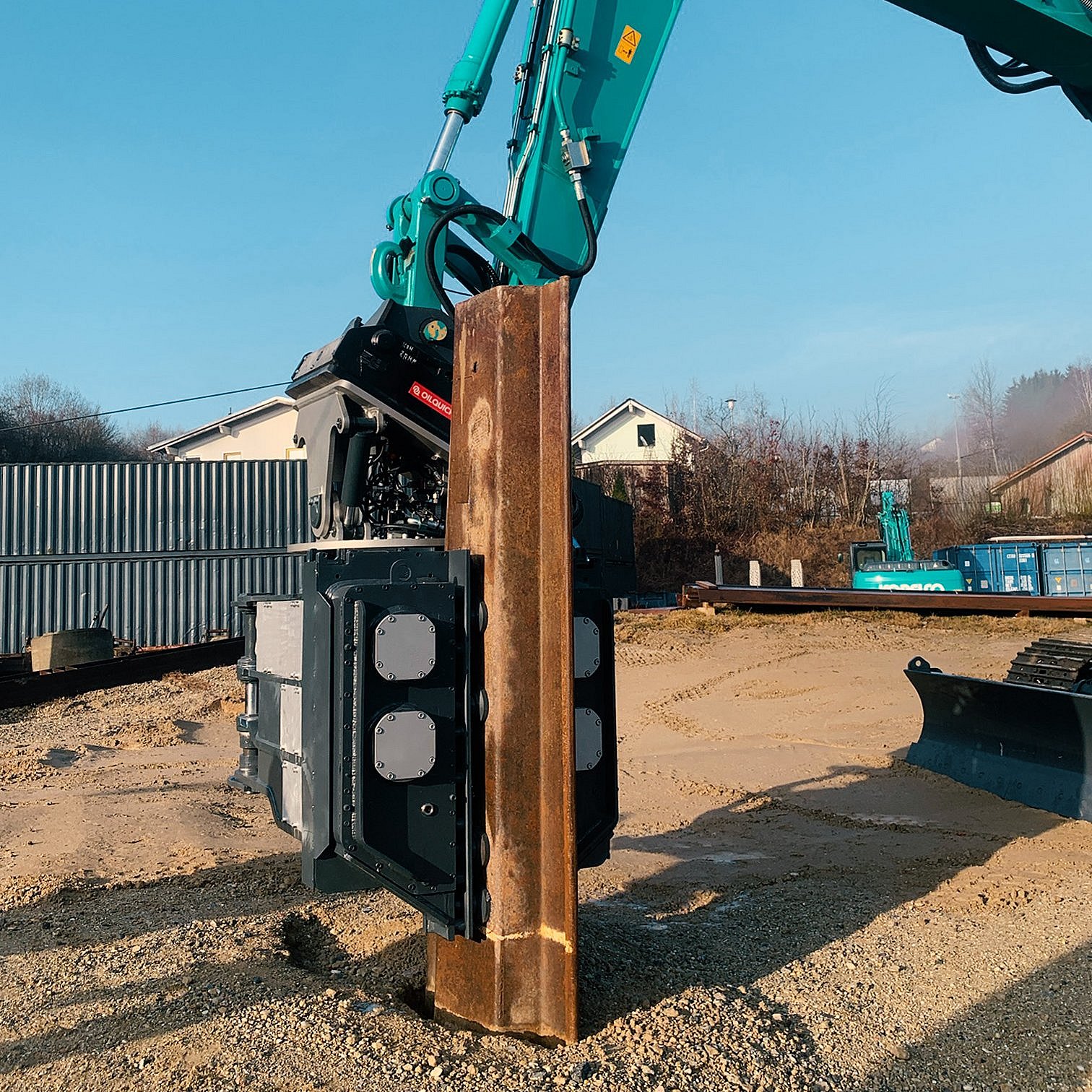
50% more powerful than any other side handle ram.
CENTRIC ⦁ HIT Technology
CENTRIC ⦁ HIT - TECHNOLOGY grips the pile centrally so that the vibration unit is positioned exactly in the centre of the pile and transmits the vibration optimally. This innovative technology ensures an even application of force, minimises material stresses and maximises the efficiency of energy transfer, making the pile-driving process more precise, powerful and gentle on the pile.
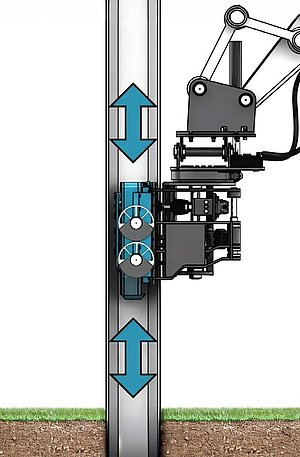
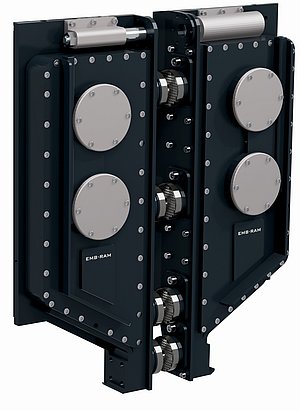
Dynamic weight
The CENTRIC ⦁ HIT - TECHNOLOGY has a 50 % lower dynamic weight than all competitors. This means that no unnecessary masses need to be accelerated. This increases energy efficiency, reduces wear and optimises the performance of the ramming process.
Avoidance of snaking lines
The CENTRIC ⦁ HIT - TECHNOLOGY ensures that snaking lines are avoided by gripping the pile in the centre. The straight-line insertion of the pile into the ground ensures precise positioning, minimises ground vibration and thus increases the efficiency and stability of the pile-driving process.

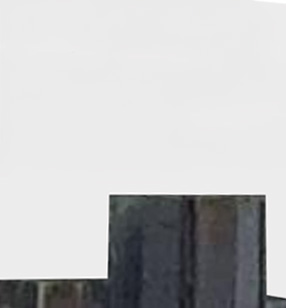
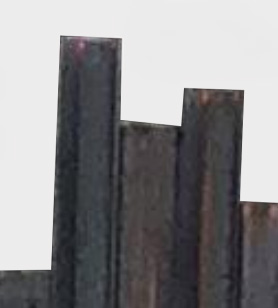
No ‘falling wall’ problem
The CENTRIC ⦁ HIT - TECHNOLOGY prevents the wall (piling/sheet pile) from ‘falling’. The centred gripping and straight-line power transmission ensure stable guidance of the pile, guaranteeing a controlled and precise driving process. This improves pile driving quality, increases safety on the construction site and enables faster, more efficient working methods.
Double linear guide
The precisely fitting double linear guide stabilises the two vibra housings so that the vibration is generated exclusively by a precise up and down movement. As a result, no undesirable axial forces are exerted on the pile, which ensures precise force transmission. This leads to a significant increase in propulsion, optimises energy transfer and maximises the efficiency of the piling process.
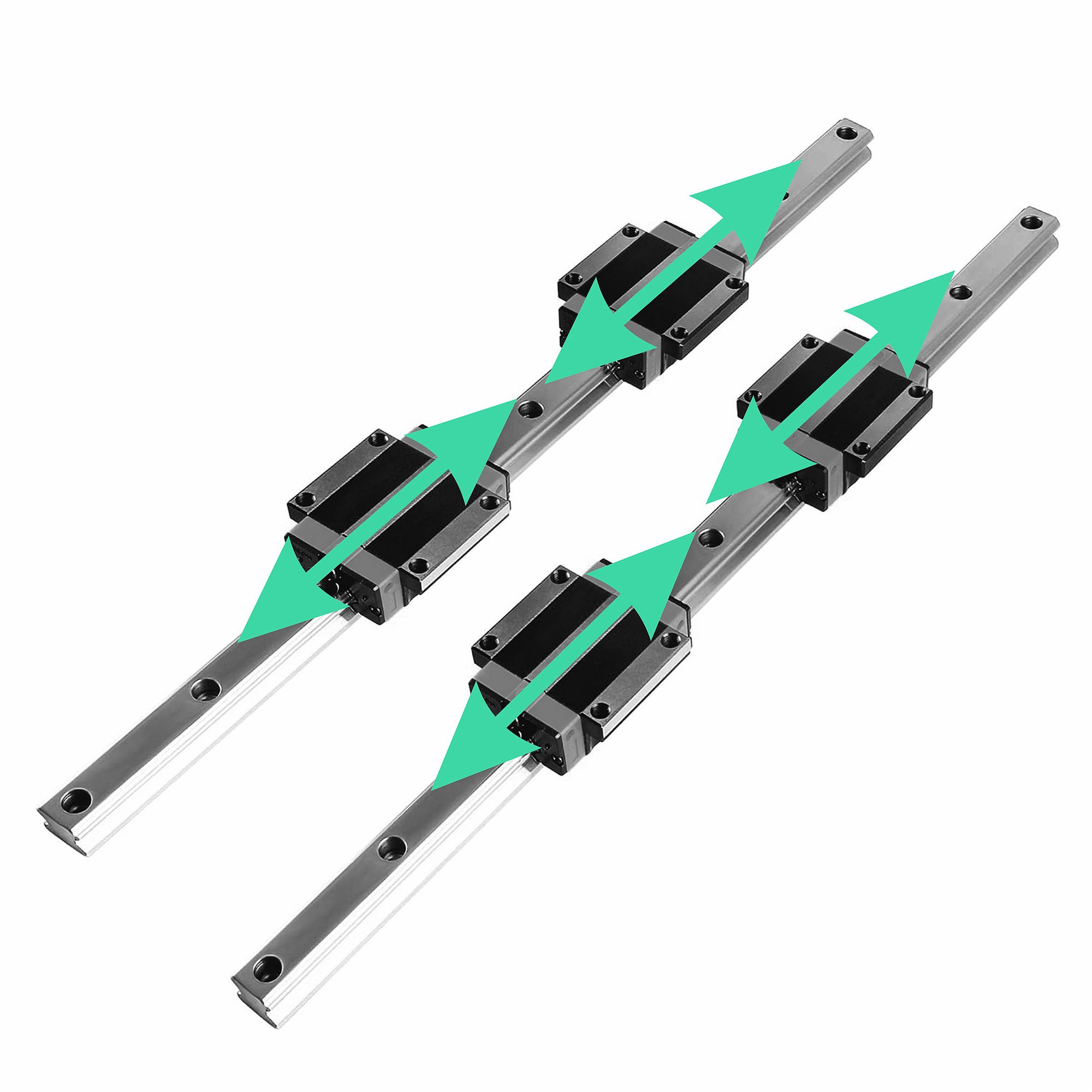
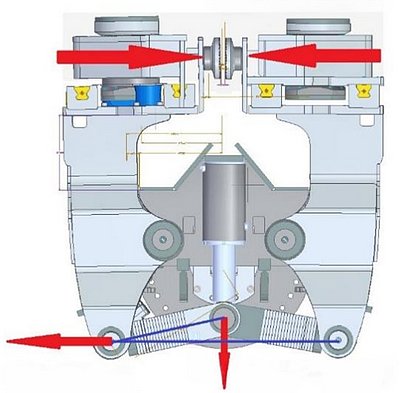
Extremely strong gripping
The CENTRIC ⦁ HIT - TECHNOLOGY enables extremely powerful and precise gripping of the pile thanks to an individually adjustable pressing force. If required, a pressing force of up to 130 tonnes can be generated, ensuring optimum vibration transmission and maximising the efficiency of the piling process. At the same time, this high pressing force minimises wear as it prevents the jaws from burning.
40% less floor vibration
No shaking of the pile
The shaking (vibrating) or swinging of the pile is one of the main causes of ground vibrations - in fact, 50-70 % of ground vibrations are due to this uncontrolled shaking.
CENTRIC ⦁ HIT - TECHNOLOGY specifically counteracts this effect. Centric gripping with high pressing force on the clamping jaws stabilises the pile, reduces unwanted vibrations and ensures that the force is applied evenly. The remaining 30-50 % of the ground vibrations are caused by the friction between the pile and the ground. Thanks to direct vibration transmission with strong, precise gripping, CENTRIC ⦁ HIT - TECHNOLOGY optimises vibration efficiency and makes a significant contribution to further minimising ground vibrations.
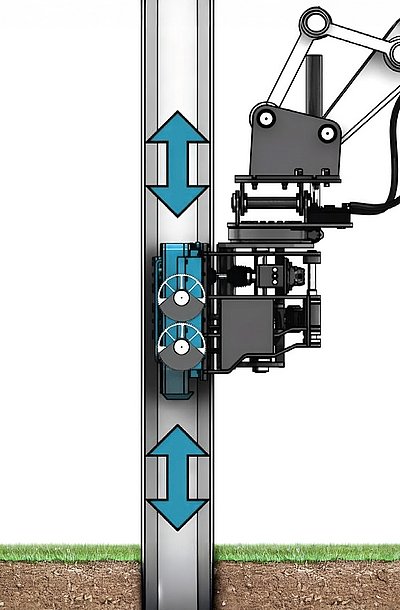

Avoidance of snaking lines
‘Snaking lines cause considerable ground vibrations and impair the precision of the pile driving process. CENTRIC ⦁ HIT -TECHNOLOGY ensures optimum stabilisation of the pile thanks to its centric and powerful gripping action. In combination with the EMB ⦁ RAM Control System, it enables the pile to be pushed through the carrier in a precise, straight line, ensuring the exact application of force. This largely prevents the snaking line effect, minimises ground vibrations and significantly increases the stability and efficiency of the piling process.
20 % less sound pollution (noise)
No noise due to shaking of the pile-driving material
The shaking of the pile produces a considerable amount of noise that pollutes the working environment and surroundings. Thanks to CENTRIC ⦁ HIT - TECHNOLOGY, this uncontrolled shaking is largely prevented by keeping the pile centred and with high pressing force. This significantly reduces noise generation, which minimises noise pollution and enables more efficient operation.
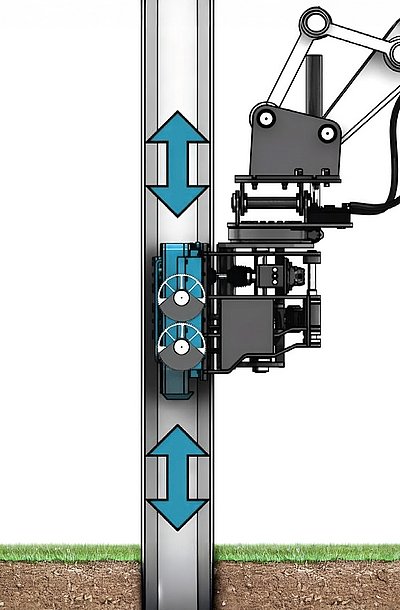
CENTRIC ⦁ HIT - Technology vs. competition
Competition (conventional technology)
With conventional systems, the vibration takes place in a range of 80-90 cm outside the pile. As a result, valuable energy is lost and the efficiency of the pile driving process is significantly impaired.
Consequences of this inefficient vibration transmission:
- Energy loss: Up to 30 % of the energy is lost as the vibration is not fully transferred to the pile.
- Snaking line effect: Uncontrolled vibrations lead to “snaking lines”, which cause increased ground vibrations and impair the precision of the ramming process.
- Material fatigue: Cracks in the arms are caused by extreme load peaks and uncontrolled vibrations.
- Component wear: Excessive stress on the rubber dampers due to overloading leads to premature damage.
EMB ⦁ RAM CENTRIC ⦁ HIT - Technology
The CENTRIC ⦁ HIT - TECHNOLOGY impresses with its particularly low dynamic weight - up to 50 % less mass compared to conventional systems.
As only the vibration housing is set in vibration, this results in decisive advantages:
- Higher performance: 50 % less mass enables 50 % higher performance,
- Efficient energy transfer: No unnecessary masses need to be accelerated.
This results in maximum energy efficiency, optimised power transmission and significantly reduced wear, which considerably improves the service life and cost-effectiveness of the system.
Competition (conventional technology)
Conventional systems have an excessively high dynamic weight, as several heavy components have to be set in vibration:
- Vibration housing
- Clamping arms with respective holders
- Hydraulic cylinders
- Hydraulic motors
The resulting disadvantages:
- Loss of power: 50 % less power, as unnecessary masses are also accelerated.
- Increased energy consumption: Reduced efficiency due to unnecessary effort.
- Higher component load: Accelerated wear and increased maintenance costs.
- Inefficient vibration transmission: Impeded propulsion of the pile-driving material.
These factors lead to significantly lower pile driving performance, higher operating costs and inefficient utilisation of the energy generated.
Practical example: Dynamic weight
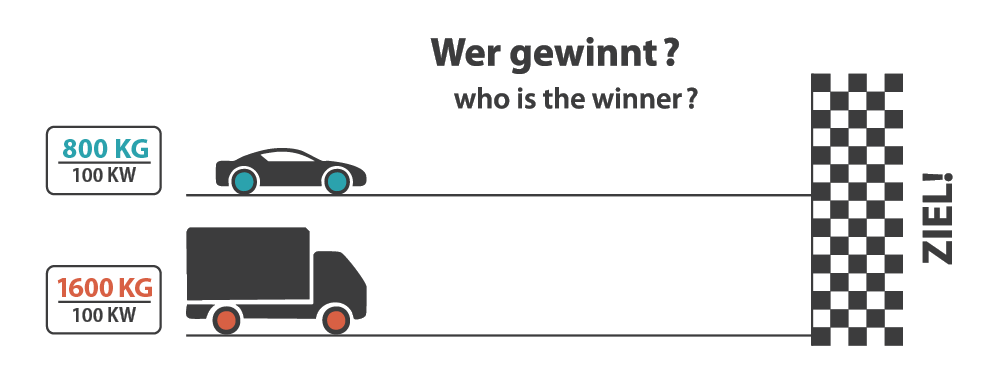
Explanation:
If two cars have the same performance, the lighter vehicle always wins, as less mass has to be moved and the energy is converted more efficiently into acceleration.
This principle also applies to ramming technology: a lower dynamic weight leads to higher performance, better energy efficiency and reduced wear, as no unnecessary masses need to be accelerated.
EMB ⦁ RAM CENTRIC ⦁ HIT - Technology
The minimised shaking of the pile-driving material significantly reduces both noise and ground vibrations, which considerably improves the efficiency and environmental compatibility of the pile-driving process.
The decisive advantages:
- Less noise emissions: Optimised working conditions and easier compliance with environmental regulations.
- Reduced ground vibrations: Minimised risk of damage to surrounding structures.
- Maximum energy efficiency: Power is channelled into driving the pile instead of being lost through uncontrolled vibrations.
The result:
A powerful, precise and environmentally friendly piling process with optimised energy transfer.
Competition: (conventional technology)
Disadvantages due to heavy shaking of the pile
A strong vibration of the pile driving material has considerable disadvantages that impair the efficiency and cost-effectiveness of the pile driving process:
- High noise level: stress on the working environment and need for additional noise protection measures.
- Strong ground vibrations: Hazard to surrounding structures and potential damage.
- Increased energy loss: A significant proportion of the vibration energy is released uncontrollably instead of being channelled into driving the pile.
- Increased maintenance costs: Faster wear of central components such as clamping jaws, hydraulic cylinders and damping elements due to additional loads.
The result:
Lower efficiency, higher operating costs and an overall less economical piling process.
EMB ⦁ RAM CENTRIC ⦁ HIT - Technology
Advantages of Centric Hit technology:
- No shaking of the pile, which prevents energy loss and unwanted vibrations.
- Low ground vibration, which protects surrounding structures and minimises environmental impact.
- Low noise, which improves working conditions and reduces noise emissions.
- Low maintenance costs due to reduced wear on clamping jaws, hydraulic cylinders and damping elements.
Competition: (conventional technology)
Disadvantages of the competition (conventional technology)
- Strong shaking of the pile-driving material
→ Energy losses and uncontrolled movements - ‘Snaking lines’
→ Uneven propulsion and increased ground vibrations - Large ground vibrations
→ Stress and possible damage to surrounding structures - High noise level
→ Impairment of the working environment and increased noise protection requirements - High friction in the locks of the pile-driving material
→ Increased material wear and possible fitting problems - Cracks in the rubber dampers
→ Excessive load due to uncontrolled vibrations - Heavy wear on the clamping jaws
→ Shortened service life due to uneven application of force - Bending and damage to the pile-driving material
→ Imprecise application of force leads to material damage
EMB ⦁ RAM CENTRIC ⦁ HIT - Technology
CENTRIC ⦁ HIT - Advantages of the special cylinder arrangement
The special arrangement of the cylinder with corresponding deflection creates an extremely high clamping force on the clamping jaws, which can be individually adjusted - up to 130 tonnes.
This results in the following advantages:
- Very good transmission of the vibration to the pile-driving material
→ Maximum efficiency and precise propulsion - No or little wear on the clamping jaws
→ Longer service life and lower replacement costs - No damage to the pile
→ Gentle but powerful clamping - Low service costs
→ Less maintenance and reduced operating costs
Competition: (conventional technology)
Competition - Standard cylinder linkage
Only 50-60 tonnes of clamping force are possible with the conventional cylinder linkage.
This leads to several disadvantages:
- Lower transmission of vibration to the pile
→ Less power and higher energy loss - High wear on the clamping jaws
→ Increased wear and shortened service life - Welding between clamping jaws and pile-driving material
→ Material build-up and impairment of function - Damage to the pile-driving material
→ Uneven clamping force can cause deformation - High service costs
→ Increased maintenance costs and more frequent repairs
Summary
Summary
CENTRIC ⦁ HIT - TECHNOLOGY revolutionizes the piling process by making the pile driving faster, more efficient and more powerful. This innovative technology ensures that the pile is captured exactly in the center, which means that the vibrations are transferred directly to the pile without any losses. The precise transmission of vibrations leads to significantly better energy efficiency during pile driving and increases the overall performance of the system.
A key advantage of this technology is the generation of high-frequency vibrations caused by the system's imbalance. These vibrations significantly reduce the resistance between the surfaces of the pile-driving material and the ground. Normally, the resistance of the ground slows down the penetration of the pile-driving material, which slows down the entire pile-driving process. However, the targeted transmission of vibrations loosens the soil material and significantly reduces the friction between the pile and the soil. The result is that the pile penetrates the soil much faster and with less energy. This leads to a considerable reduction in overall working time, which is a great advantage both on construction sites and from an economic point of view. In addition, the energy consumption of the entire system is significantly reduced, which also makes the technology very advantageous from an ecological point of view.
Another key advantage of CENTRIC ⦁ HIT - TECHNOLOGY is the minimization of ground vibrations. Traditional pile driving techniques often generate strong vibrations that can be transmitted to neighboring buildings and sensitive infrastructure and cause damage. In urban areas, where sensitive buildings and infrastructure are prevalent, minimizing these vibrations is of particular importance. However, centric gripping and the controlled transmission of vibrations drastically reduce the effect of ground vibrations. This makes CENTRIC ⦁ HIT - TECHNOLOGY a particularly safe and environmentally friendly solution for the piling process.
An additional advantage of the centric gripping technique is the avoidance of so-called “snaking lines”, which occur when the pile is not gripped centrically. Snaking lines lead to uncontrolled movement of the pile-driving material and can severely impair the precision of the pile-driving process. Centric gripping prevents this problem, as the vibrations act evenly and without losses on the pile. As a result, the pile remains in a stable position and is driven into the ground with greater precision and uniformity.
A decisive factor for the exceptional performance of CENTRIC ⦁ HIT - TECHNOLOGY is the low dynamic weight of the vibration housing. In contrast to conventional pile drivers, where weight plays a major role, the reduced weight of the system enables faster and more precise transmission of vibrations. This means that less mass needs to be moved to achieve the same effect, resulting in an increase in performance of at least 50 %. This increase in performance results not only in a higher speed of the ramming process, but also in a longer service life of the entire system, as less mechanical stress is exerted on the vibration housing. In addition, the lower weight contributes to a further reduction in energy consumption, resulting in long-term cost savings.
Conclusion
CENTRIC ⦁ HIT - TECHNOLOGY offers a number of advantages that significantly improve both the efficiency and environmental compatibility of the piling process. The fast and precise transfer of vibrations to the pile, the reduction in resistance between the pile and the ground and the minimization of ground vibrations and snaking lead to a significant improvement in overall performance. The reduced dynamic weight also ensures an increase in performance and greater energy efficiency. This combination makes CENTRIC ⦁ HIT - TECHNOLOGY an innovative and extremely promising solution for the modern piling process.
EXCENTERMOMENT
High frequency side grip vibrating pile driver
(2300-3000 rpm / 38-50 Hz)
Specially designed for use with various carriers.
- Constant and efficient vibration due to fixed eccentric torque.
- Minimisation of ground vibrations thanks to extremely fast start-up and braking of the unbalance.
- Optimised energy transfer, as the natural frequency of the ground is quickly ‘driven through’.
This technology makes the piling process more efficient and environmentally friendly.
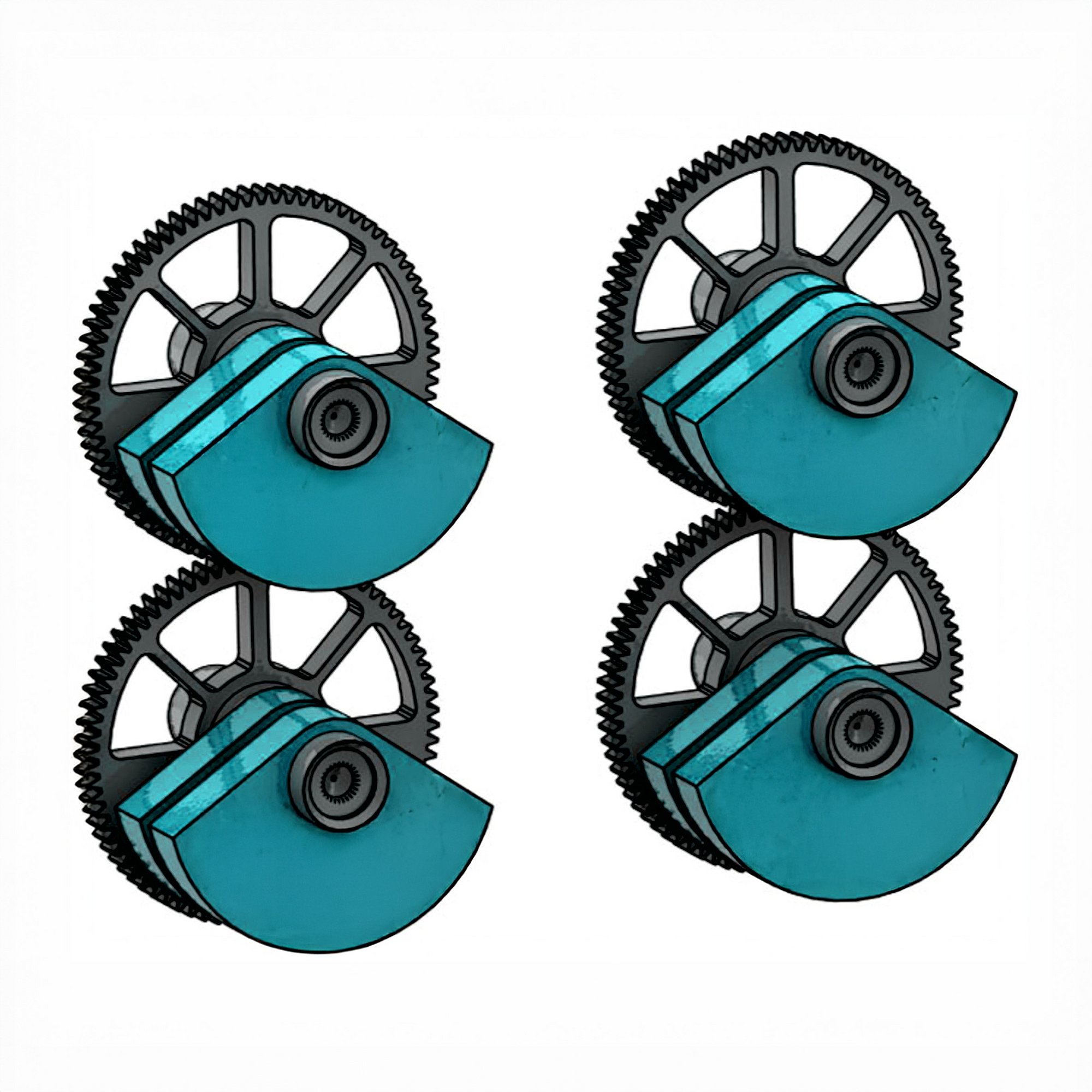
High frequency operation
High frequency operation
The EMB ⦁ RAM side handle attachment vibrators are equipped with a fixed eccentric torque that ensures constant and efficient vibration. This design enables precise control of the pile-driving force and ensures that the vibrator remains consistently powerful throughout the entire work process.
An outstanding feature of the EMB ⦁ RAM attachment vibrators is the use of high-frequency operation, which typically includes frequencies above 38 Hz. This high frequency makes a decisive contribution to minimising disruptive influences on the environment. By setting the vibrations of the vibrator to a frequency that does not match the natural frequency of the surrounding structures, the risk of vibration resonance, which could lead to structural damage or disruptive vibrations, is virtually eliminated.
Another advantage of high-frequency operation is the extremely fast start-up of the unbalance. This rapid acceleration means that the natural frequency of the surrounding structures is ‘passed through’ so quickly that vibrations are minimised. This means that the vibrations generated during operation of the vibrator are significantly reduced, which greatly reduces the impact on neighbouring buildings or infrastructure.
In addition to the reduced vibration, the EMB ⦁ RAM side handle mounted vibrators are characterised by a significant reduction in noise. The EMB ⦁ RAM generates significantly less noise than conventional vibrators, which is particularly beneficial in urban or noise-sensitive environments. This makes for a more pleasant working environment and contributes to compliance with noise protection regulations.
Last but not least, the EMB ⦁ RAM side handle mounted vibrators offer faster and more comfortable handling thanks to their optimised technology. The devices are more efficient, take less time to use and offer the operator an improved user experience as the whole process is smoother and requires less effort.
EMB ⦁ RAM Control System
Safety
The EMB ⦁ RAM Control System precisely displays the Z-axis at all times, while the X- and Y-axes are clearly visible on the pile.
This visual display ensures maximum safety as it enables clear and precise alignment so that no person is required in the danger zone. At the same time, it ensures high efficiency by carrying out the piling process in a precise and controlled manner.
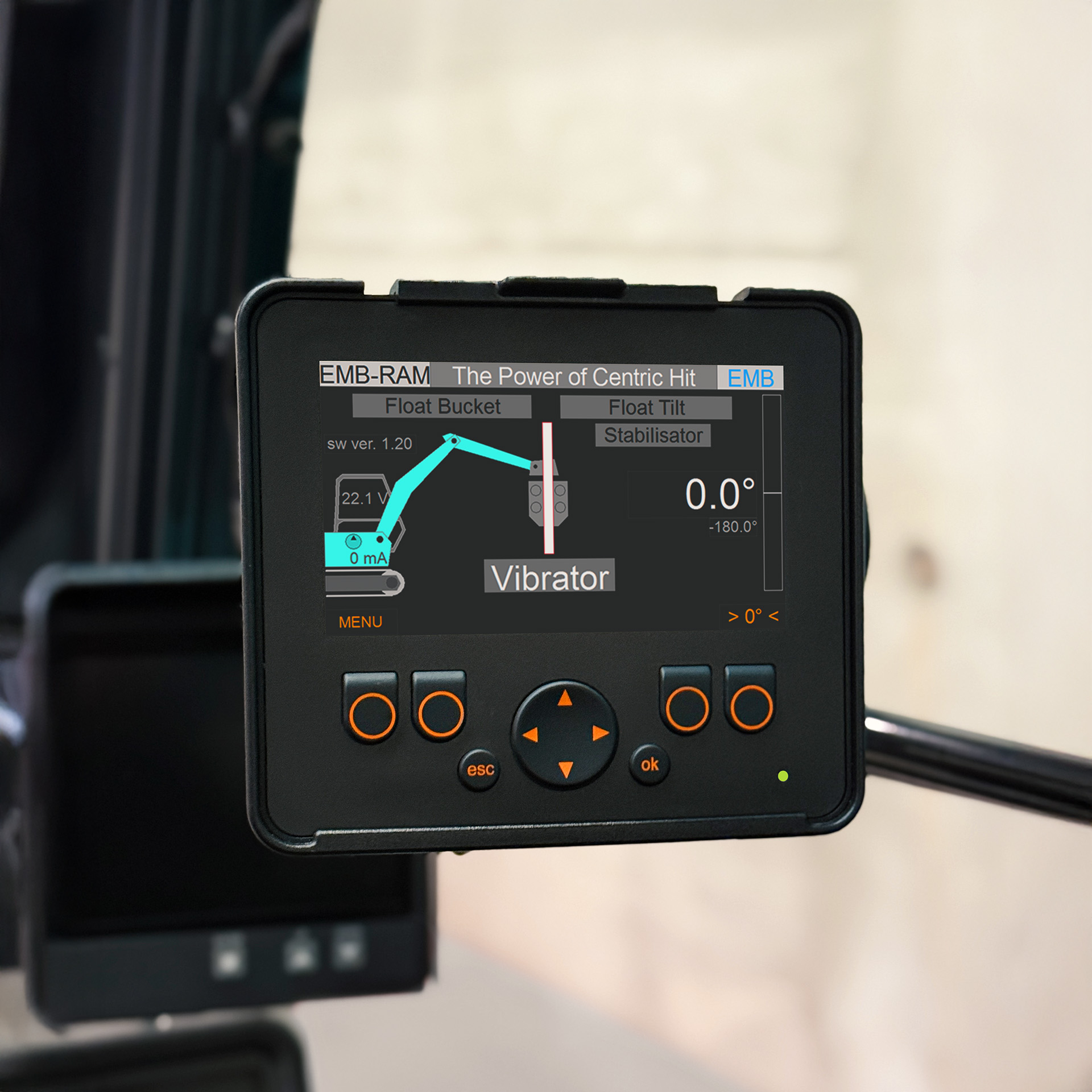
EMB ⦁ RAM Control System
EMB ⦁ RAM Control System
The EMB ⦁ RAM side grip attachment vibrator is operated and controlled by the sophisticated EMB ⦁ RAM CONTROL SYSTEM, which acts as the central interface between the excavator and the attachment vibrator. This system ensures a seamless connection and communication between the two devices, guaranteeing optimum and efficient operation. The EMB ⦁ RAM CONTROL SYSTEM is attached both to the carrier and directly to the EMB ⦁ RAM side grip attachment vibrator, enabling precise control and monitoring of all functions.
The EMB ⦁ RAM CONTROL SYSTEM controls the excavator's auxiliary hydraulics and enables precise regulation of all functions of the attachment vibrator. It ensures that all movements and settings of the side grip attachment vibrator are carried out smoothly and in real time. This includes controlling the eccentric movements for precise adjustment of the vibration intensity and the targeted activation and deactivation of specific control aids, tailored to the requirements of the respective piling process.
Thanks to this intelligent control technology, the EMB ⦁ RAM CONTROL SYSTEM not only ensures high performance and efficiency, but also contributes to increased safety and reduced machine wear, as the functions of the attachment vibrator are always optimally adapted to the conditions on the construction site.
Joysticks
Joystick´s
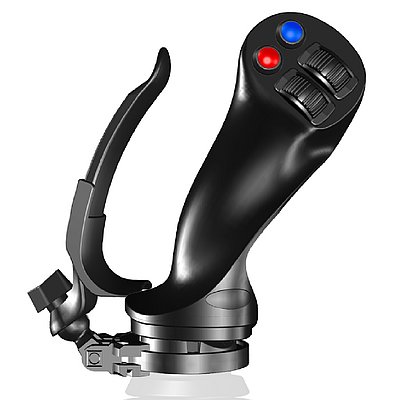
Left Joystick
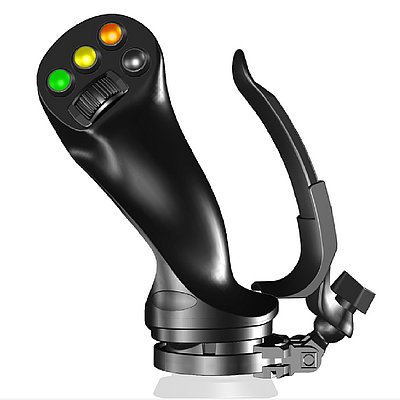
Right Joystick
Aktive Steuerung
Active control
When the vibration is activated on the joystick, the EMB ⦁ RAM CONTROL SYSTEM actively intervenes and, depending on the vibration mode selected, sets either the bucket tipping cylinder or both the bucket tipping cylinder and the tilt cylinder to the floating position. This makes it much easier for the pile to penetrate the ground and automatically prevents the formation of snaking lines to minimise ground vibrations.
The system is also equipped with a safety cut-out, which ensures that the floating function or vibration is only activated when the appropriate counter-pressure is applied. This means that the pile must be in clear contact with the ground and sufficiently pressed in before the process starts.
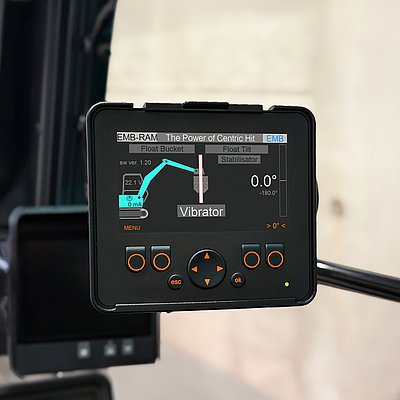
Safety
The EMB ⦁ RAM Control System precisely displays the Z-axis at all times, while the X- and Y-axes are clearly visible on the pile.
This visual display ensures maximum safety, as it enables clear and precise alignment so that no person is required in the danger zone. At the same time, it ensures high efficiency by carrying out the piling process in a precise and controlled manner.
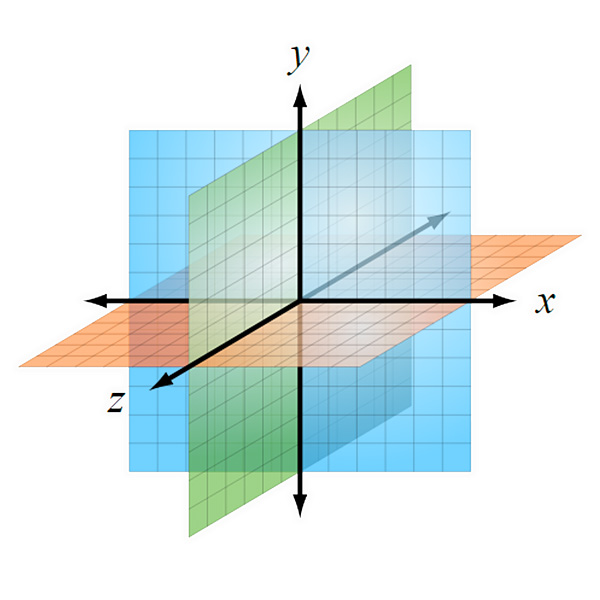
EMB ⦁ RAM Lubrication
The highly developed lubrication system for the Vibra bearings, inspired by racing, ensures optimum cooling and lubrication. The targeted supply of lubricant reduces friction, extends the service life of the bearings and minimises wear.
The innovative cooling technology keeps the operating temperature stable and prevents overheating, even under high loads. As a result, the performance of the system remains consistently high and downtimes are reduced.
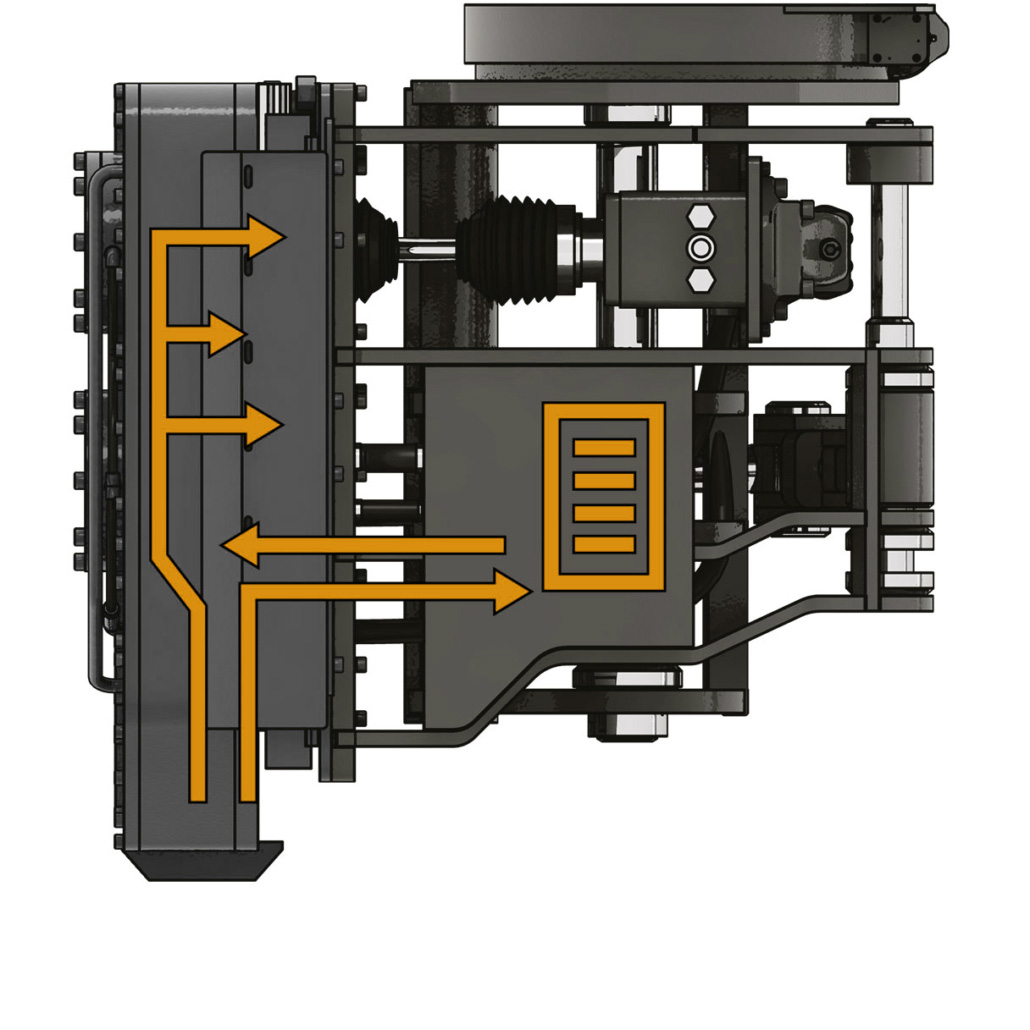
Lubrication & cooling system
EMB ⦁ RAM LUBRICATION SYSTEM
LUBRICATION SYSTEM OF THE EMB ⦁ RAM:
The EMB ⦁ RAM side handle mounted vibrators are equipped with a sophisticated lubrication system designed to optimise both the lubrication of the moving components and the temperature regulation of the entire system. The targeted use of modern technology ensures that all critical components are supplied with sufficient lubricant at all times, reducing friction and minimising wear. At the same time, the system helps to efficiently dissipate the heat generated to prevent the mechanical elements from overheating and ensure consistently high vibrator performance.
The lubrication system is based on a sophisticated circuit that is supported by two specially designed oil pumps. These pumps ensure that the lubricating oil circulates continuously and reaches exactly where it is needed. In addition, two external oil tanks are integrated into the system, which ensure a constant supply of fresh oil and also serve as a reservoir for cooling and degassing the lubricant. This design enables an even distribution of the oil within the product and prevents insufficient lubrication of individual components, especially under demanding operating conditions or high loads.
This advanced lubrication technology not only optimises the
Video - Lubrication and cooling system
Maintenance & wear
30 % lower maintenance and repair costs
Thanks to state-of-the-art technologies and optimised components, maintenance and repair costs are reduced by up to 30%. The high efficiency and durability of the EMB ⦁ RAM side handle vibrators minimise wear and reduce the need for repairs.
CENTRIC ⦁ HIT - TECHNOLOGY reduces mechanical loads and uncontrolled vibrations through precise, centric power transmission, which significantly reduces material wear.
The intelligent lubrication system ensures optimum lubrication and cooling of central components, extends the service life of the machine and reduces operating costs in the long term.
30 % lower maintenance and repair costs
30 % lower maintenance and repair costs
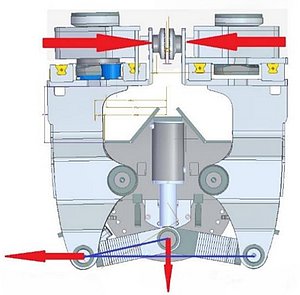
Extremely strong gripping
CENTRIC ⦁ HIT - Advantages of the special cylinder arrangement
The special arrangement of the cylinder with corresponding deflection creates an extremely high clamping force on the clamping jaws, which can be individually adjusted - up to 130 tonnes.
This results in the following advantages:
- Very good transmission of the vibration to the pile-driving material
→ Maximum efficiency and precise propulsion - No or little wear on the clamping jaws
→ Longer service life and lower replacement costs - No damage to the pile
→ Gentle but powerful clamping - Low service costs
→ Less maintenance and reduced operating costs
EMB ⦁ RAM CENTRIC ⦁ HIT - Technology

Advantages of CENTRIC ⦁ HIT Technology
- No shaking of the pile, which prevents energy losses and unwanted vibrations.
- Low ground vibration, which protects surrounding structures and minimises environmental impact.
- Low noise, which improves working conditions and reduces noise emissions.
- Low maintenance costs due to reduced wear on clamping jaws, hydraulic cylinders and damping elements.
Competition (conventional technology)
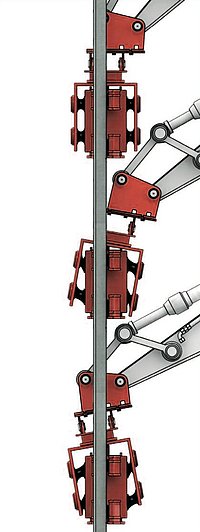
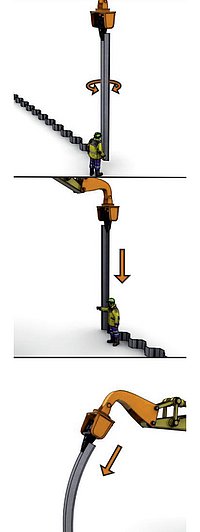
Disadvantages of the competition (conventional technology)
- Strong shaking of the pile-driving material
→ Energy losses and uncontrolled movements - ‘Snaking lines’
→ Uneven propulsion and increased ground vibrations - Large ground vibrations
→ Stress and possible damage to surrounding structures - High noise level
→ Impairment of the working environment and increased noise protection requirements - High friction in the locks of the pile-driving material
→ Increased material wear and possible fitting problems - Cracks in the rubber dampers
→ Excessive load due to uncontrolled vibrations - Heavy wear on the clamping jaws
→ Shortened service life due to uneven application of force - Bending and damage to the pile-driving material
→ Imprecise application of force leads to material damage
Active control
When the vibration is activated on the joystick, the EMB ⦁ RAM Control System actively intervenes and, depending on the vibration mode selected, sets either the bucket tipping cylinder or both the bucket tipping cylinder and the tilt cylinder to the floating position. This makes it much easier for the pile to penetrate the ground and automatically prevents the formation of snaking lines to minimise ground vibrations.
The system is also equipped with a safety cut-out, which ensures that the floating function or vibration is only activated when the appropriate counter-pressure is applied. This means that the pile must be in clear contact with the ground and sufficiently pressed in before the process starts.
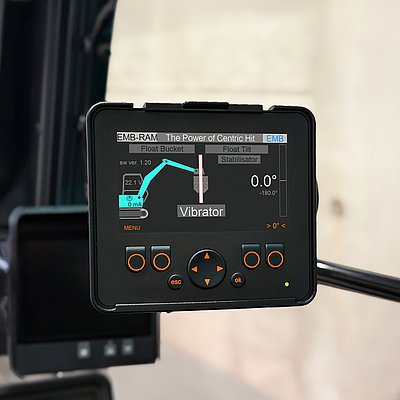
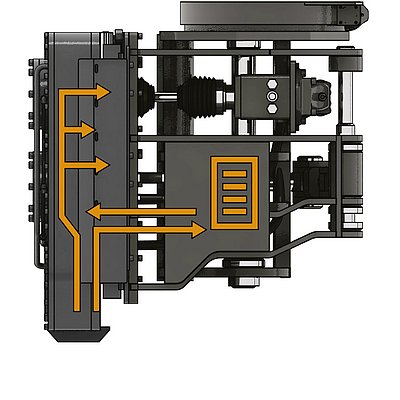
EMB ⦁ RAM LUBRICATION SYSTEM
EMB ⦁ RAM LUBRICATION SYSTEM
This advanced lubrication technology not only significantly extends the service life of the components, but also improves the efficiency and reliability of the entire mounted vibrator. The system ensures smooth operation, minimises the risk of unplanned downtime and makes a significant contribution to the operational safety and performance of the machine.