For CARRIER DEVICES
The EMB ⦁ RAM is suitable for various carriers, including excavators from 14 to 58 tonnes. It makes optimum use of the carrier's hydraulic power and lifting capacity for an efficient and powerful piling process.
Developed for use with all wheeled and crawler excavators as well as track vehicles, the EMB ⦁ RAM can be operated with the standard auxiliary hydraulics of the carrier and via its hydraulic or electronic control system. This ensures precise handling and a high level of operational safety.
Thanks to Centric ⦁ Hit technology, the EMB ⦁ RAM offers reliable performance in demanding conditions. The wide compatibility with various excavator types ensures maximum versatility and economy.
COMPREHENSIVE RANGE OF MODELS AND SIZES
The EMB ⦁ RAM is available in a variety of models, sizes and configurations to provide a customised solution for a wide range of pile types and requirements. It is suitable for steel sheet piles, round or rectangular support profiles as well as plastic or concrete piles and wooden piles.
Thanks to its high flexibility and versatility, the EMB ⦁ RAM ensures efficient and precise piling processes in a wide range of applications.
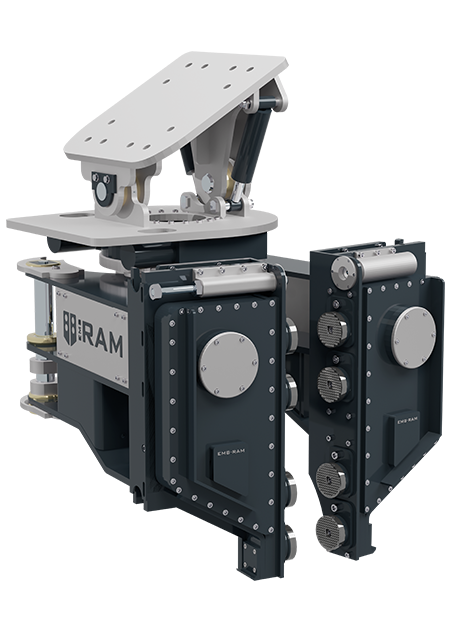
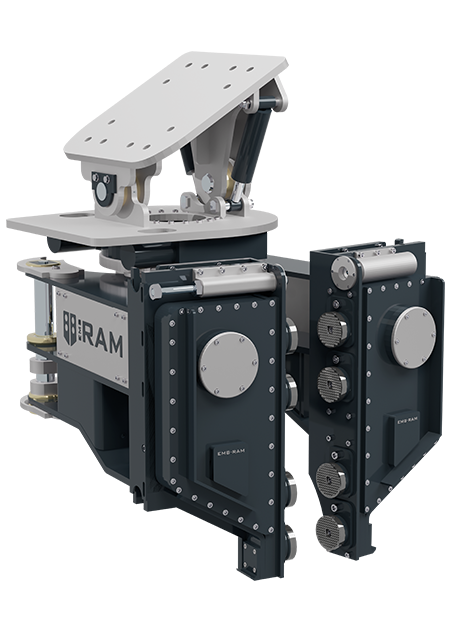
Technical data
(All technical data is subject to change by the manufacturer at any time without prior notice.)
EMB ⦁ RAM model (Centric ⦁ Hit)
1600R
2100R
2700R
3000R
4000R
5000R
EMB ⦁ RAM model (Centric ⦁ Hit):
Weight (without adapter)
:
(kg)
1600R:
2.130
2100R:
2.570
2700R:
2.780
3000R:
2.940
4000R:
3.290
5000R:
3.880
EMB ⦁ RAM model (Centric ⦁ Hit):
Height
:
(mm)
1600R:
1.890
2100R:
1.921
2700R:
2.018
3000R:
2.018
4000R:
2.018
5000R:
2.230
EMB ⦁ RAM model (Centric ⦁ Hit):
Depth
:
(mm)
1600R:
1.372
2100R:
1.372
2700R:
1.458
3000R:
1.458
4000R:
1.458
5000R:
1.790
EMB ⦁ RAM model (Centric ⦁ Hit):
Width
:
(mm)
1600R:
1.875
2100R:
1.875
2700R:
1.875
3000R:
1.875
4000R:
1.875
5000R:
2.019
EMB ⦁ RAM model (Centric ⦁ Hit):
Hydraulic power
:
(kW)
1600R:
69
2100R:
108
2700R:
108
3000R:
108
4000R:
136
5000R:
185
EMB ⦁ RAM model (Centric ⦁ Hit):
Max. Oil flow carrier unit
:
(l/min)
1600R:
140
2100R:
190
2700R:
190
3000R:
190
4000R:
240
5000R:
280
EMB ⦁ RAM model (Centric ⦁ Hit):
Nominal operating pressure
:
(bar)
1600R:
250-280
2100R:
250-280
2700R:
250-280
3000R:
250-280
4000R:
250-280
5000R:
250-280
EMB ⦁ RAM model (Centric ⦁ Hit):
Max. Return pressure
:
(bar)
1600R:
5 - 8
2100R:
5 - 8
2700R:
5 - 8
3000R:
5 - 8
4000R:
5 - 8
5000R:
5 - 8
EMB ⦁ RAM model (Centric ⦁ Hit):
Pressure setting of carrier device
:
(bar)
1600R:
340
2100R:
340
2700R:
340
3000R:
340
4000R:
340
5000R:
340
EMB ⦁ RAM model (Centric ⦁ Hit):
Min. motor power of carrier unit
:
(kW)
1600R:
85
2100R:
125
2700R:
145
3000R:
180
4000R:
200
5000R:
310
EMB ⦁ RAM model (Centric ⦁ Hit):
Frequency
:
(1/min.)
1600R:
2.300-3.000
2100R:
2.300-3.000
2700R:
2.300-3.000
3000R:
2.300-3.000
4000R:
2.300-3.000
5000R:
2.300-3.000
EMB ⦁ RAM model (Centric ⦁ Hit):
Max. Centrifugal force
:
(kN)
1600R:
500
2100R:
600
2700R:
650
3000R:
770
4000R:
820
5000R:
930
EMB ⦁ RAM model (Centric ⦁ Hit):
Swivel angle / tilt angle
:
(°)
1600R:
360 / +/-38
2100R:
360 / +/-38
2700R:
360 / +/-38
3000R:
360 / +/-38
4000R:
360 / +/-38
5000R:
360 / +/-38
EMB ⦁ RAM model (Centric ⦁ Hit):
Drive method
:
1600R:
vibtration
2100R:
vibtration
2700R:
vibtration
3000R:
vibtration
4000R:
vibtration
5000R:
vibtration
EMB ⦁ RAM model (Centric ⦁ Hit):
Max. Sheet pile length
:
(m)
1600R:
16
2100R:
16
2700R:
16
3000R:
16
4000R:
16
5000R:
16
EMB ⦁ RAM model (Centric ⦁ Hit):
Max. pipe diameter
:
(mm)
1600R:
800
2100R:
800
2700R:
800
3000R:
800
4000R:
800
5000R:
1200
EMB ⦁ RAM model (Centric ⦁ Hit):
Excavator class
:
(t)
1600R:
14-19
2100R:
20-24
2700R:
23-29
3000R:
30-34
4000R:
35-48
5000R:
43-60
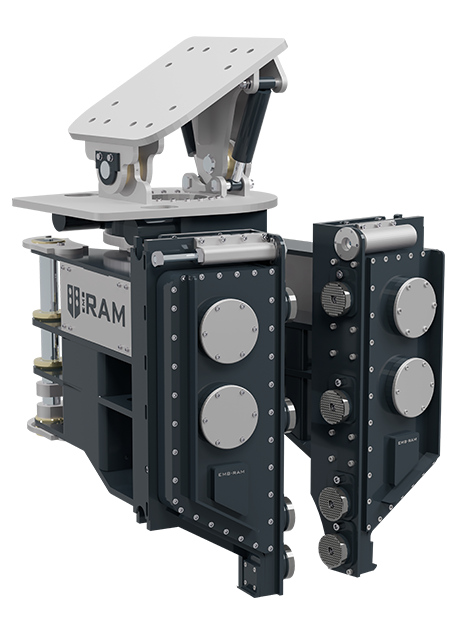
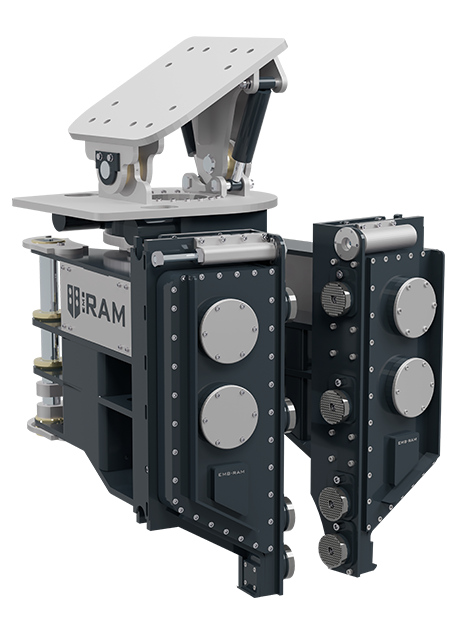
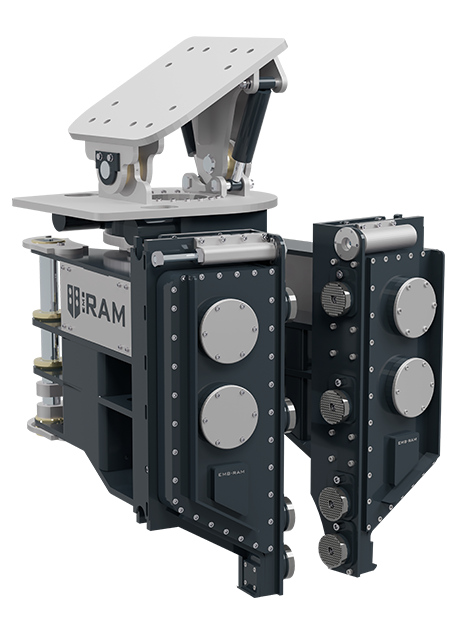
Technical data
(All technical data is subject to change by the manufacturer at any time without prior notice.)
EMB ⦁ RAM model (Centric ⦁ Hit)
1600R
2100R
2700R
3000R
4000R
5000R
EMB ⦁ RAM model (Centric ⦁ Hit):
Weight (without adapter)
:
(kg)
1600R:
2.130
2100R:
2.570
2700R:
2.780
3000R:
2.940
4000R:
3.290
5000R:
3.880
EMB ⦁ RAM model (Centric ⦁ Hit):
Height
:
(mm)
1600R:
1.890
2100R:
1.921
2700R:
2.018
3000R:
2.018
4000R:
2.018
5000R:
2.230
EMB ⦁ RAM model (Centric ⦁ Hit):
Depth
:
(mm)
1600R:
1.372
2100R:
1.372
2700R:
1.458
3000R:
1.458
4000R:
1.458
5000R:
1.790
EMB ⦁ RAM model (Centric ⦁ Hit):
Width
:
(mm)
1600R:
1.875
2100R:
1.875
2700R:
1.875
3000R:
1.875
4000R:
1.875
5000R:
2.019
EMB ⦁ RAM model (Centric ⦁ Hit):
Hydraulic power
:
(kW)
1600R:
69
2100R:
108
2700R:
108
3000R:
108
4000R:
136
5000R:
185
EMB ⦁ RAM model (Centric ⦁ Hit):
Max. Oil flow carrier unit
:
(l/min)
1600R:
140
2100R:
190
2700R:
190
3000R:
190
4000R:
240
5000R:
280
EMB ⦁ RAM model (Centric ⦁ Hit):
Nominal operating pressure
:
(bar)
1600R:
250-280
2100R:
250-280
2700R:
250-280
3000R:
250-280
4000R:
250-280
5000R:
250-280
EMB ⦁ RAM model (Centric ⦁ Hit):
Max. Return pressure
:
(bar)
1600R:
5 - 8
2100R:
5 - 8
2700R:
5 - 8
3000R:
5 - 8
4000R:
5 - 8
5000R:
5 - 8
EMB ⦁ RAM model (Centric ⦁ Hit):
Pressure setting of carrier device
:
(bar)
1600R:
340
2100R:
340
2700R:
340
3000R:
340
4000R:
340
5000R:
340
EMB ⦁ RAM model (Centric ⦁ Hit):
Min. motor power of carrier unit
:
(kW)
1600R:
85
2100R:
125
2700R:
145
3000R:
180
4000R:
200
5000R:
310
EMB ⦁ RAM model (Centric ⦁ Hit):
Frequency
:
(1/min.)
1600R:
2.300-3.000
2100R:
2.300-3.000
2700R:
2.300-3.000
3000R:
2.300-3.000
4000R:
2.300-3.000
5000R:
2.300-3.000
EMB ⦁ RAM model (Centric ⦁ Hit):
Max. Centrifugal force
:
(kN)
1600R:
500
2100R:
600
2700R:
650
3000R:
770
4000R:
820
5000R:
930
EMB ⦁ RAM model (Centric ⦁ Hit):
Swivel angle / tilt angle
:
(°)
1600R:
360 / +/-38
2100R:
360 / +/-38
2700R:
360 / +/-38
3000R:
360 / +/-38
4000R:
360 / +/-38
5000R:
360 / +/-38
EMB ⦁ RAM model (Centric ⦁ Hit):
Drive method
:
1600R:
vibtration
2100R:
vibtration
2700R:
vibtration
3000R:
vibtration
4000R:
vibtration
5000R:
vibtration
EMB ⦁ RAM model (Centric ⦁ Hit):
Max. Sheet pile length
:
(m)
1600R:
16
2100R:
16
2700R:
16
3000R:
16
4000R:
16
5000R:
16
EMB ⦁ RAM model (Centric ⦁ Hit):
Max. pipe diameter
:
(mm)
1600R:
800
2100R:
800
2700R:
800
3000R:
800
4000R:
800
5000R:
1200
EMB ⦁ RAM model (Centric ⦁ Hit):
Excavator class
:
(t)
1600R:
14-19
2100R:
20-24
2700R:
23-29
3000R:
30-34
4000R:
35-48
5000R:
43-60
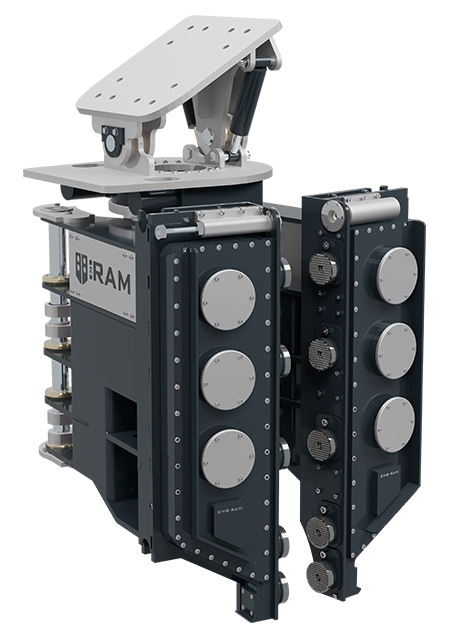
Technical data
(All technical data is subject to change by the manufacturer at any time without prior notice.)
EMB ⦁ RAM model (Centric ⦁ Hit)
1600R
2100R
2700R
3000R
4000R
5000R
EMB ⦁ RAM model (Centric ⦁ Hit):
Weight (without adapter)
:
(kg)
1600R:
2.130
2100R:
2.570
2700R:
2.780
3000R:
2.940
4000R:
3.290
5000R:
3.880
EMB ⦁ RAM model (Centric ⦁ Hit):
Height
:
(mm)
1600R:
1.890
2100R:
1.921
2700R:
2.018
3000R:
2.018
4000R:
2.018
5000R:
2.230
EMB ⦁ RAM model (Centric ⦁ Hit):
Depth
:
(mm)
1600R:
1.372
2100R:
1.372
2700R:
1.458
3000R:
1.458
4000R:
1.458
5000R:
1.790
EMB ⦁ RAM model (Centric ⦁ Hit):
Width
:
(mm)
1600R:
1.875
2100R:
1.875
2700R:
1.875
3000R:
1.875
4000R:
1.875
5000R:
2.019
EMB ⦁ RAM model (Centric ⦁ Hit):
Hydraulic power
:
(kW)
1600R:
69
2100R:
108
2700R:
108
3000R:
108
4000R:
136
5000R:
185
EMB ⦁ RAM model (Centric ⦁ Hit):
Max. Oil flow carrier unit
:
(l/min)
1600R:
140
2100R:
190
2700R:
190
3000R:
190
4000R:
240
5000R:
280
EMB ⦁ RAM model (Centric ⦁ Hit):
Nominal operating pressure
:
(bar)
1600R:
250-280
2100R:
250-280
2700R:
250-280
3000R:
250-280
4000R:
250-280
5000R:
250-280
EMB ⦁ RAM model (Centric ⦁ Hit):
Max. Return pressure
:
(bar)
1600R:
5 - 8
2100R:
5 - 8
2700R:
5 - 8
3000R:
5 - 8
4000R:
5 - 8
5000R:
5 - 8
EMB ⦁ RAM model (Centric ⦁ Hit):
Pressure setting of carrier device
:
(bar)
1600R:
340
2100R:
340
2700R:
340
3000R:
340
4000R:
340
5000R:
340
EMB ⦁ RAM model (Centric ⦁ Hit):
Min. motor power of carrier unit
:
(kW)
1600R:
85
2100R:
125
2700R:
145
3000R:
180
4000R:
200
5000R:
310
EMB ⦁ RAM model (Centric ⦁ Hit):
Frequency
:
(1/min.)
1600R:
2.300-3.000
2100R:
2.300-3.000
2700R:
2.300-3.000
3000R:
2.300-3.000
4000R:
2.300-3.000
5000R:
2.300-3.000
EMB ⦁ RAM model (Centric ⦁ Hit):
Max. Centrifugal force
:
(kN)
1600R:
500
2100R:
600
2700R:
650
3000R:
770
4000R:
820
5000R:
930
EMB ⦁ RAM model (Centric ⦁ Hit):
Swivel angle / tilt angle
:
(°)
1600R:
360 / +/-38
2100R:
360 / +/-38
2700R:
360 / +/-38
3000R:
360 / +/-38
4000R:
360 / +/-38
5000R:
360 / +/-38
EMB ⦁ RAM model (Centric ⦁ Hit):
Drive method
:
1600R:
vibtration
2100R:
vibtration
2700R:
vibtration
3000R:
vibtration
4000R:
vibtration
5000R:
vibtration
EMB ⦁ RAM model (Centric ⦁ Hit):
Max. Sheet pile length
:
(m)
1600R:
16
2100R:
16
2700R:
16
3000R:
16
4000R:
16
5000R:
16
EMB ⦁ RAM model (Centric ⦁ Hit):
Max. pipe diameter
:
(mm)
1600R:
800
2100R:
800
2700R:
800
3000R:
800
4000R:
800
5000R:
1200
EMB ⦁ RAM model (Centric ⦁ Hit):
Excavator class
:
(t)
1600R:
14-19
2100R:
20-24
2700R:
23-29
3000R:
30-34
4000R:
35-48
5000R:
43-60
EMB ⦁ RAM - modular system Options / Features
The EMB ⦁ RAM is characterised by its innovative modular system, which offers exceptional versatility and adaptability. Thanks to its flexible design, the same unit can be used for a wide range of requirements, pile types and working conditions. This enables greater efficiency, shortens changeover times and increases productivity on a wide variety of construction sites.
Thanks to its optimised design, the EMB ⦁ RAM can be quickly and easily adapted to changing operating conditions, making it a particularly economical and future-proof solution for a wide range of piling projects.
Clamping jaw extension for H-beams
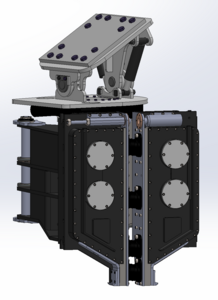
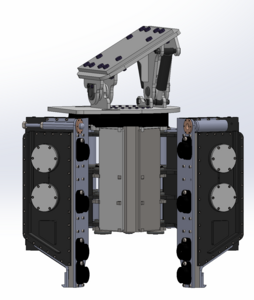
without jaw extension
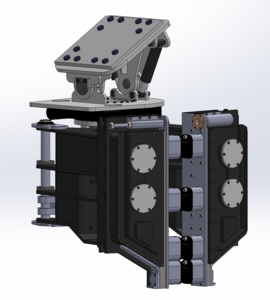
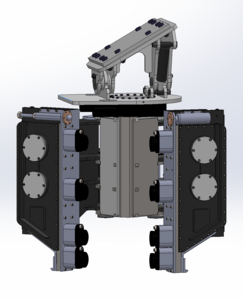
with jaw extension
(6 cm/12 cm/18 cm/24 cm)
Sheet piles - lifter
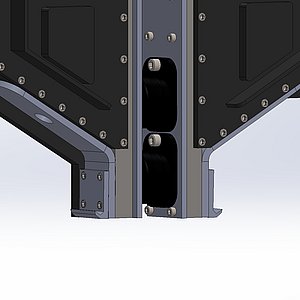
Sheet piles - hoes
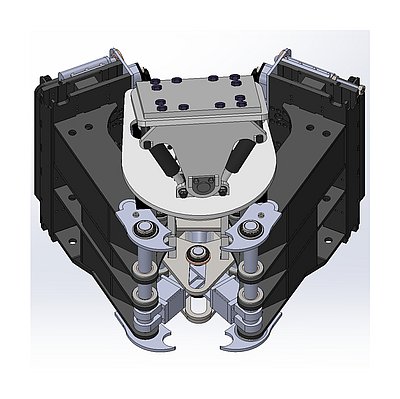
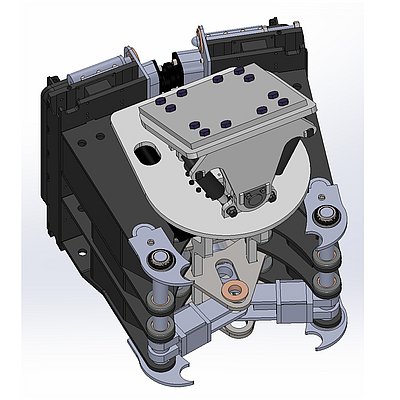
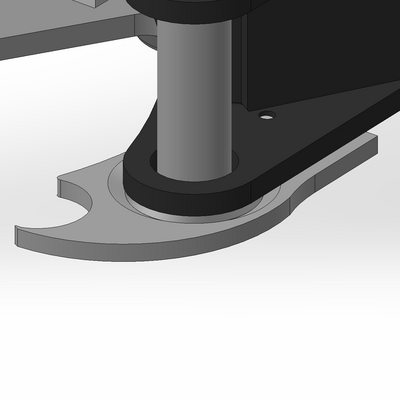
H-beam - lifter
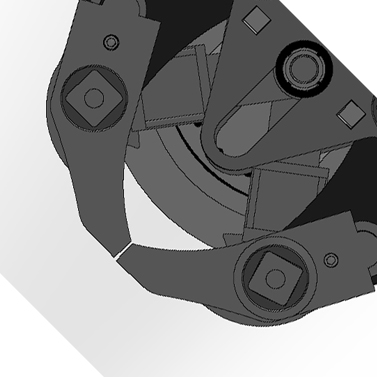
Pipe pile clamps (for steel, cast iron, concrete, wood)

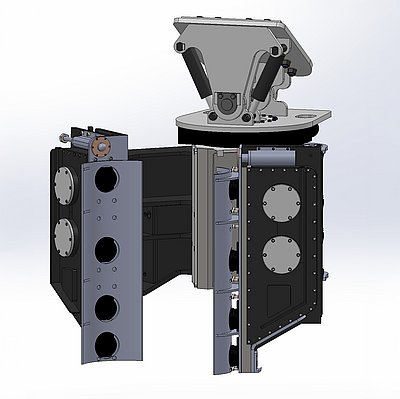
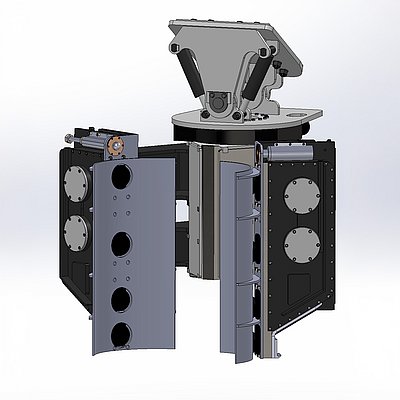
Requirements for the carrier device
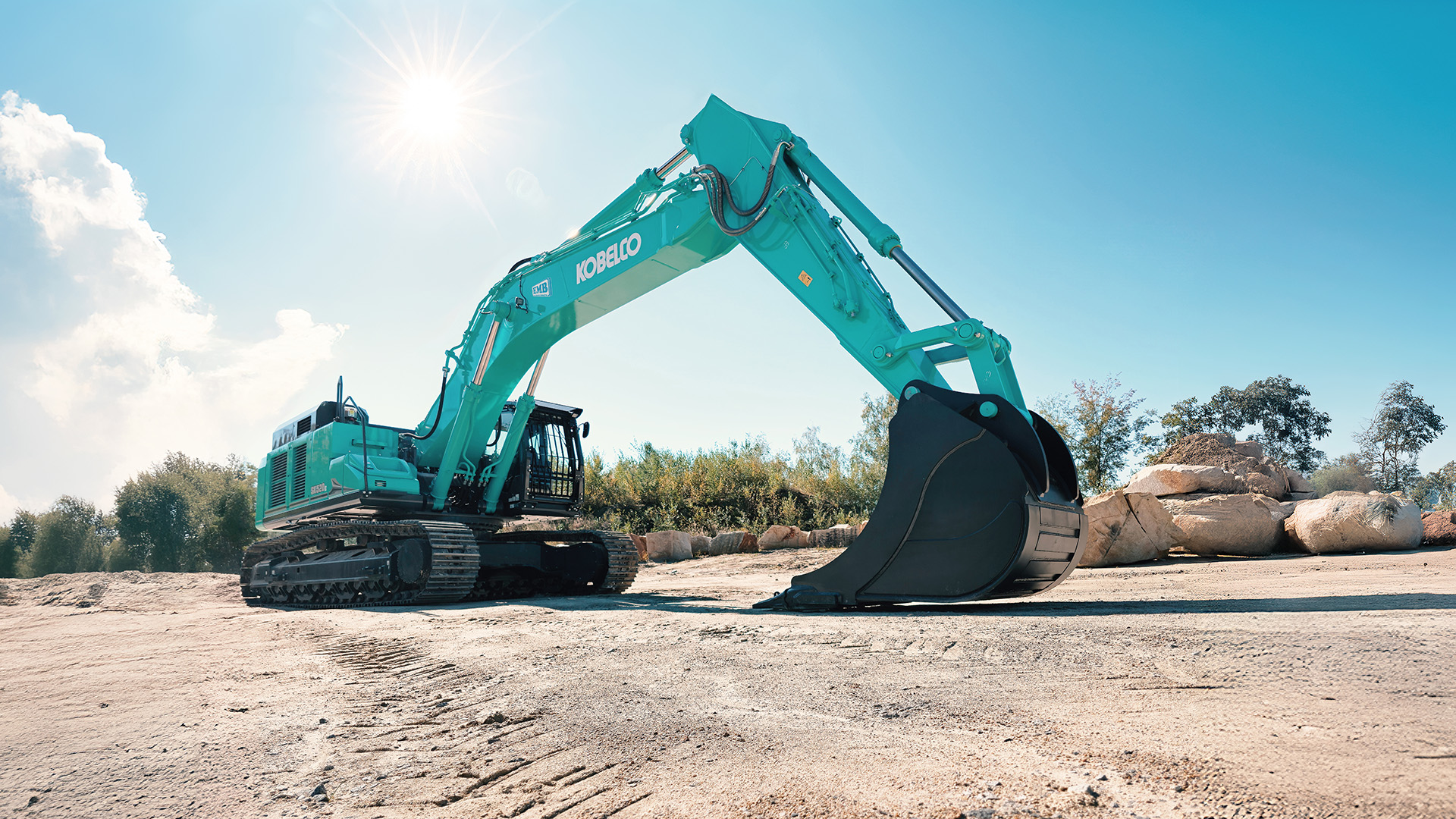
Requirements for the carrier device
REQUIREMENTS FOR THE CARRIER
The EMB ⦁ RAM side grip attachment vibrators and the EMB Up/Down Hammer, developed and distributed by EMB Baumaschinen Handelsgesellschaft mbH, have been specially designed to be mounted and efficiently operated on a wide range of conventional excavators. Their design enables seamless integration into the carrier's hydraulic system, ensuring high compatibility and optimum power transmission.
The connection to the carrier's auxiliary hydraulic system is made via standardised interfaces, which ensures a secure and stable connection. However, if installation on special carrier machines such as road-rail excavators or other special vehicles is required, it is advisable to contact EMB Baumaschinen Handelsgesellschaft mbH in advance. The company provides detailed technical specifications and customisation solutions to ensure perfect integration even with non-standardised machines.
In order for the EMB ⦁ RAM to function properly and ensure long-term operational safety, the excavator must fulfil certain technical requirements. These requirements are not only of central importance for the performance of the device, but also form the basis for the warranty. Improper installation or inadequate hydraulic requirements could lead to malfunctions, increased wear or even damage to the carrier and the EMB ⦁ RAM.
To ensure safe installation and trouble-free operation, it is strongly recommended that an oil flow measurement is carried out on the intended carrier unit before installing an EMB ⦁ RAM implement. This measurement ensures that the excavator's hydraulic system can provide the required flow rate and pressure to operate the unit efficiently and at maximum performance. Further details on the specific requirements and test procedures are listed in Appendix 2.
IMPORTANT:
The installation of the EMB ⦁ RAM may only be carried out by a specialist dealer authorised by EMB Baumaschinen Handelsgesellschaft mbH!
IMPORTANT:
REQUIREMENTS FOR THE STABILITY (STABILITY IN USE) OF THE CARRIER: When selecting the carrier for use with an EMB ⦁ RAM, it is essential to ensure that it is sufficiently stable and stable during operation. The technical specification of the carrier device must be consulted for assessment. The permissible total weight of the EMB ⦁ RAM, including quick coupler and piling material, must never exceed the maximum lifting load limit specified for the carrier !!!! A load table with the permissible lifting capacities can be found on the inside window of the cab as well as in the technical specification of the carrier. The device operator is responsible for adhering to the load limits in order to ensure safe operation and stable operation.
A) GENERAL DESCRIPTION
The hammer valve and the valve for the lifting function of the carrier device must be supplied via separate oil pumps so that a separate pump connection is provided for each individual function.
Basic principle of hydraulic separation
For perfect functioning and maximum performance, it is essential that the hydraulic circuit of the lifting function of the carrier device is completely separate from the hydraulic circuit of the EMB ⦁ RAM. This ensures that both systems work independently of each other, which prevents power losses, uncontrolled pressure fluctuations and disruptions to the operating process.
It is also very advantageous if the uppercarriage slewing function of the carrier is not operated via the same hydraulic circuit to which the EMB ⦁ RAM is connected. A separate supply reduces the risk of pressure drops or power losses and ensures stable and reliable hydraulic performance during the ramming process.
The EMB ⦁ RAM generally works within an operating pressure range of 240 to 290 bar. The exact target specifications for pressure and flow rate are listed in detail in Appendix 2 and must be observed during installation and operation of the device in order to ensure optimum performance and a long service life of the hydraulic components. This is a fundamental requirement for maintaining the warranty.
B) OIL FLOW RATE (litres/min.)
Required oil flow rate for the EMB ⦁ RAM
The oil flow rate required for safe and efficient operation of the EMB ⦁ RAM is detailed in the following table on the next page. To ensure optimum performance and operational safety, it is recommended that the oil flow rate is set approximately 5 % higher than the value actually required. This recommended oil flow rate ensures that the EMB-RAM is sufficiently supplied with hydraulic oil at all times and that power losses are avoided. The oil flow rate is always measured under operating pressure conditions of the EMB ⦁ RAM in order to enable a realistic assessment of the hydraulic requirements (see following table).
Important note on the oil flow and pressure requirements
It should be noted that the hydraulic requirements, particularly with regard to oil flow and operating pressure, may differ depending on the EMB ⦁ RAM model. Therefore, the specific technical requirements of the respective model should be taken into account to ensure optimum performance.
Basic principle for maintaining the oil flow rate
For stable operation and to avoid malfunctions, it is recommended to keep the oil flow rate within a tolerance range of +/-5 %. This recommendation also takes into account the parallel use of other excavator functions that also require hydraulic power. An insufficient or strongly fluctuating oil flow rate can impair the performance of the EMB ⦁ RAM and lead to inefficient operation.
Influence of pressure on the oil flow rate
The oil flow rate specified in the technical data generally refers to a measurement at 0 bar pressure. In practice, however, the performance curve of a hydraulic oil pump shows that the actual oil flow rate gradually decreases as the pressure increases. This is due to the physical properties of the hydraulic system, in particular the pressure compensation of the pump (pump control).
It is therefore particularly important to bear in mind that the It is therefore particularly important to bear in mind that the EMB ⦁ RAM always requires the maximum oil flow rate at nominal operating pressure to ensure full performance. If the oil flow rate is too low, the EMB ⦁ RAM may not work with the required force or may move more slowly, which could impair efficiency and productivity. always requires the maximum oil flow rate at nominal operating pressure to ensure full performance. If the oil flow rate is too low, the EMB ⦁ RAM may not work with the required force or may move more slowly, which could impair efficiency and productivity.
Detailed information on the required and recommended oil flow rate for the various EMB ⦁ RAM models can be found in the following table:
EMB ⦁ RAM model
Excavator class (tonnes)
Setting value of the overpressure valve, excavator max. (bar (g) )
Nominal operating pressure of EMB-RAM (bar(g))
Max. Oil flow EMB-RAM (l/min)
Max. Oil flow EMB-RAM (l/min)
EMB-RAM power (kW)
Min. pressure hose/pipe size
Min. return hose/pipe size
EMB ⦁ RAM model:
1600 R
Excavator class (tonnes):
14-19 to.
Setting value of the overpressure valve, excavator max. (bar (g) ):
320
Nominal operating pressure of EMB-RAM (bar(g)):
250 - 280
Max. Oil flow EMB-RAM (l/min):
140
Max. Oil flow EMB-RAM (l/min):
58
EMB-RAM power (kW):
85
Min. pressure hose/pipe size:
NW20 (mm) ¾“
Min. return hose/pipe size:
NW25 (mm) 1“
EMB ⦁ RAM model:
2100 R
Excavator class (tonnes):
20-24 to.
Setting value of the overpressure valve, excavator max. (bar (g) ):
320
Nominal operating pressure of EMB-RAM (bar(g)):
250 - 280
Max. Oil flow EMB-RAM (l/min):
180
Max. Oil flow EMB-RAM (l/min):
85
EMB-RAM power (kW):
125
Min. pressure hose/pipe size:
NW25 (mm) 1“
Min. return hose/pipe size:
NW25 (mm) 1“
EMB ⦁ RAM model:
2700 R
Excavator class (tonnes):
25-29 to.
Setting value of the overpressure valve, excavator max. (bar (g) ):
320
Nominal operating pressure of EMB-RAM (bar(g)):
250 - 280
Max. Oil flow EMB-RAM (l/min):
180
Max. Oil flow EMB-RAM (l/min):
93
EMB-RAM power (kW):
145
Min. pressure hose/pipe size:
NW25 (mm) 1“
Min. return hose/pipe size:
NW32 (mm) 1¼“
EMB ⦁ RAM model:
3000 R
Excavator class (tonnes):
30-34 to.
Setting value of the overpressure valve, excavator max. (bar (g) ):
320
Nominal operating pressure of EMB-RAM (bar(g)):
250 - 280
Max. Oil flow EMB-RAM (l/min):
180
Max. Oil flow EMB-RAM (l/min):
119
EMB-RAM power (kW):
180
Min. pressure hose/pipe size:
NW32 (mm) 1¼“
Min. return hose/pipe size:
NW38 (mm) 1½“
EMB ⦁ RAM model:
4000 R
Excavator class (tonnes):
35-42 to.
Setting value of the overpressure valve, excavator max. (bar (g) ):
320
Nominal operating pressure of EMB-RAM (bar(g)):
250 - 280
Max. Oil flow EMB-RAM (l/min):
240
Max. Oil flow EMB-RAM (l/min):
130
EMB-RAM power (kW):
200
Min. pressure hose/pipe size:
NW32 (mm) 1¼“
Min. return hose/pipe size:
NW38 (mm) 1½“
EMB ⦁ RAM model:
5000 R
Excavator class (tonnes):
43-55 to.
Setting value of the overpressure valve, excavator max. (bar (g) ):
320
Nominal operating pressure of EMB-RAM (bar(g)):
250 - 280
Max. Oil flow EMB-RAM (l/min):
280
Max. Oil flow EMB-RAM (l/min):
185
EMB-RAM power (kW):
310
Min. pressure hose/pipe size:
NW38 (mm) 1½“
Min. return hose/pipe size:
NW50 (mm) 2“
ATTENTION:
The selected carrier device must comply with the guidelines of the lifting capacity and stability table as well as all safety-related specifications of the manufacturer. In addition, it must be ensured that the oil flow rate and pressure settings fully comply with the specifications and technical guidelines of EMB Baumaschinen Handelsgesellschaft mbH in order to guarantee efficient and safe operation.
PRESCRIBED OIL QUANTITY MEASUREMENT ON THE CARRIER DEVICE
Before installing the EMB ⦁ RAM, it is mandatory that a thorough oil flow measurement is carried out on the carrier intended for operating the EMB ⦁ RAM. This check is essential to ensure that the hydraulic delivery capacity of the carrier device meets the technical requirements of the EMB ⦁ RAM.
In addition to measuring the oil quantity, the maximum pressure setting in the hydraulic working circuit ‘hammer’ should also be checked and adjusted if necessary. This measure serves to prevent possible malfunctions or damage to the EMB ⦁ RAM and the carrier device. An incorrect or insufficient oil flow rate can significantly impair the performance of the EMB ⦁ RAM, while excessive pressure and an excessive amount of oil can lead to damage to hydraulic components.
The oil quantity measurement should be carried out using a calibrated oil quantity measuring device suitable for the respective oil quantity. The test device is connected between the pressure line and the return line of the hammer connections on the carrier device. Care must be taken to ensure that the measuring device is installed correctly in order to obtain precise measured values.
Finally, it is prescribed that the measurement and adjustment of the hydraulic parameters is only carried out by trained specialist personnel from an authorised dealer. This ensures that the EMB ⦁ RAM is operated under optimum conditions and that maximum performance and a long service life are guaranteed.
The oil quantity measurement is carried out step by step in 20 bar, starting at 20 bar and continuously increasing to 350 bar, without interruptions. This procedure ensures precise measurement of the flow rate under different pressure conditions and enables an accurate assessment of the performance of the hydraulic system.
The primary valve of the hammer circuit must be set to 350 bar during the entire measurement in order to obtain consistent and comparable results. The permissible operating pressure should be within a range of at least 310 bar to a maximum of 350 bar. If deviations are detected, the hydraulic system must be adjusted or maintained accordingly.
During the measurement, it is necessary to simultaneously record and document the return pressure in detail. The return pressure provides valuable information about possible flow losses and any bottlenecks in the hydraulic system that could affect the overall performance.
All measured values must be carefully recorded in an oil quantity measurement report, for example in TABLE 2, in order to ensure comprehensive analysis and subsequent traceability of the results. This documentation serves as a basis for optimisation measures and ensures that the system operates within the recommended operating parameters.
C) OIL RETURN FLOW (MAX.)
The return pressure applied to the hydraulic line at the inlet of the EMB ⦁ RAM must remain within a certain range to ensure optimum performance and safe operation. At an oil temperature between 20 and 40 °C, this pressure must not exceed a maximum value of 5-8 bar. A higher return pressure can impair the hydraulic circuit and lead to undesirable performance losses.
Basic rule:
A return pressure that exceeds 13 bar has a significant impact on the functionality of the pile driver. Such a high pressure can reduce the vibrating force by up to 10 %, which significantly reduces the efficiency and performance of the system. There is also a risk of damaging the seals of the hydraulic components, which can lead to leaks, premature wear or even complete failure of the unit. It is therefore crucial to carefully monitor the return pressure and keep it within the recommended limits.
Connection and installation of the hydraulic lines:
To ensure reliable operation of the EMB ⦁ RAM, the return hose of the hydraulic line must be connected directly to the return filter of the hydraulic oil tank. It must be ensured that this hose is never routed via the main valve, as is often the case with the 2-way hydraulic line for rams. Incorrect routing of the return line can lead to pressure build-up and excessive heating of the hydraulic oil, which in turn can impair the performance of the entire system.
Before installing the EMB ⦁ RAM, it is essential that the hydraulic lines (HAMMER CIRCUIT) are fully and correctly installed on your excavator and ready for operation. The unit can only work correctly and damage to the system can only be avoided if the hydraulic supply has been properly connected.
In addition, the hoses and lines used must be sufficiently dimensioned to ensure the required oil flow for the EMB ⦁ RAM hydraulics without pressure losses or restrictions. An insufficient hose size can impede the flow, which in turn can lead to power losses, overheating or increased wear. The exact minimum sizes for the hoses and lines are detailed in TABLE #1.
D) PRESSURE SETTING (MAX.)
The pressure in the hydraulic line from the carrier must be set exactly to the value specified in TABLE 1 to ensure optimum performance and safe operation. An incorrect pressure setting can reduce the efficiency of the pile driver or cause damage to the hydraulic system. Too high a pressure increases the load on the hydraulic components and can lead to excessive wear of the seals. Too low a pressure reduces the vibrating force and impairs the performance of the pile driver.
The pressure settings vary depending on the EMB ⦁ RAM model and must be adjusted according to the technical specifications. A regular check of the values is necessary to ensure proper function and to avoid unnecessary strain or damage. If you are unsure, you should consult your EMB-RAM specialist dealer or EMB Baumaschinen Handelsgesellschaft mbH.
E) CONTROLLING THE HAMMER VALVE (CARRIER DEVICE)
The hammer valve of the carrier is controlled via the EMB ⦁ RAM Control control system, which enables precise and efficient control of the hydraulic functions. This system ensures optimum adjustment of the hydraulic power to the requirements of the pile driver and guarantees reliable operation. Depending on the version, the EMB ⦁ RAM Control control system can be controlled either via a 24 V control signal or via proportional hydraulic activation. This enables flexible integration into various carrier configurations and ensures even, controlled power transmission.
F) QUICK COUPLINGS FOR THE HYDRAULIC HOSES
Important: Do not use quick-release couplings for the hydraulic hoses, as this could restrict the oil flow. This can impair the performance of the hydraulic system and, in the worst case, lead to damage to the components. Instead, suitable, permanently installed fittings should be used to ensure a reliable and efficient hydraulic connection.